¡Bienvenido a mi blog!
Antes de profundizar en el contenido, me encantaría que me acompañaras en mis redes sociales, donde comparto más información, interactúo con la comunidad y publico actualizaciones. Puedes conectar conmigo de la siguiente manera:
Facebook:https://www.facebook.com/profile.php?id=61573740643310
Ahora, comencemos nuestro viaje juntos. Espero que el contenido aquí les resulte interesante, interesante y valioso.
Tabla de contenido
Introducción
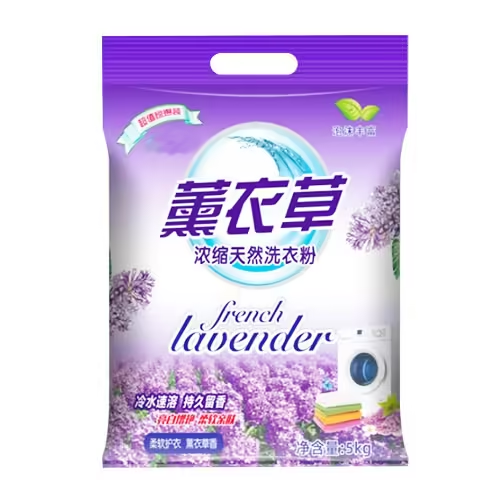
En el mercado actual, dinámico y altamente competitivo, empresas de diversos sectores recurren al plástico personalizado para impulsar la innovación, mejorar la funcionalidad de sus productos y satisfacer las demandas de los consumidores. Los plásticos personalizados ofrecen una versatilidad inigualable, lo que permite a las empresas crear soluciones a medida que se adaptan a necesidades específicas, ya sea en el sector del embalaje, la automoción, la medicina o los bienes de consumo. Al aprovechar la flexibilidad de los plásticos personalizados, las empresas pueden lograr productos rentables, duraderos y estéticamente atractivos que destaquen en el mercado. Este blog explora el potencial transformador de los plásticos personalizados, profundizando en sus aplicaciones, beneficios y cómo pueden generar nuevas oportunidades para su negocio.
Por qué los plásticos personalizados están revolucionando el desarrollo de productos
Los plásticos personalizados se han convertido en un pilar de la fabricación moderna gracias a su adaptabilidad y eficiencia. A diferencia de los plásticos estándar, los plásticos personalizados están diseñados para cumplir especificaciones precisas, lo que permite a las empresas crear productos funcionales y únicos. Desde componentes automotrices ligeros hasta dispositivos médicos complejos, los plásticos personalizados permiten personalizar propiedades del material como la resistencia, la flexibilidad y la resistencia térmica. Este nivel de personalización garantiza que los productos no solo cumplan con los estándares de la industria, sino que también superen las expectativas del cliente, impulsando la innovación y la diferenciación.
El papel del plástico personalizado en la sostenibilidad
La sostenibilidad es una preocupación creciente en todas las industrias, y los plásticos personalizados desempeñan un papel fundamental para abordar este desafío. Al optimizar el uso de materiales e incorporar opciones reciclables o biodegradables, los plásticos personalizados ayudan a reducir los residuos y el impacto ambiental. Los fabricantes pueden diseñar productos con un mínimo de material, manteniendo la durabilidad, contribuyendo así a una economía circular. Por ejemplo, los plásticos personalizados utilizados en envases pueden diseñarse para ser ligeros pero robustos, lo que reduce las emisiones de transporte y los costos de material.
Personalización para un rendimiento mejorado
Una de las características destacadas del plástico personalizado es la posibilidad de ajustar sus propiedades para adaptarlas a aplicaciones específicas. Ya sea para crear un plástico resistente al calor para piezas de automóviles o un material biocompatible para implantes médicos, el plástico personalizado permite un control preciso de características como la resistencia a la tracción, la flexibilidad y la resistencia química. Esta personalización garantiza que los productos funcionen óptimamente en sus entornos previstos, mejorando la fiabilidad y la satisfacción del cliente.
Aplicaciones clave de los plásticos personalizados en diferentes industrias
Los plásticos personalizados se utilizan en una amplia gama de industrias, cada una con sus propiedades únicas. En la industria del embalaje, se utilizan para crear botellas, contenedores y películas que protegen los productos y mejoran su atractivo en los estantes. En el sector automotriz, contribuyen a la fabricación de componentes ligeros que mejoran el consumo de combustible. La industria médica utiliza plásticos personalizados para dispositivos estériles y biocompatibles, mientras que los fabricantes de bienes de consumo los utilizan para productos duraderos y estéticamente atractivos. Estas aplicaciones demuestran la versatilidad y el impacto transformador del plástico personalizado.
Soluciones de embalaje con plásticos personalizados
La industria del embalaje ha experimentado avances significativos gracias a los plásticos personalizados. Desde botellas moldeadas por soplado hasta envases moldeados por inyección, los plásticos personalizados permiten la creación de envases funcionales y visualmente atractivos. Estas soluciones se adaptan a las necesidades específicas de cada producto, como cierres de seguridad o diseños ligeros, lo que garantiza la seguridad del producto y la comodidad del consumidor.
Innovaciones automotrices impulsadas por plásticos personalizados
En la industria automotriz, los plásticos personalizados están revolucionando el diseño de vehículos al reducir el peso y mejorar el consumo de combustible. Componentes como tableros, parachoques y paneles interiores suelen fabricarse con plásticos personalizados diseñados para ofrecer durabilidad y resistencia a los impactos. Estos materiales también permiten diseños complejos que mejoran tanto la estética como la funcionalidad, lo que proporciona a los fabricantes una ventaja competitiva.
Beneficios de elegir plásticos personalizados para su negocio
La adopción de plásticos personalizados ofrece numerosas ventajas a las empresas que buscan innovar y mantenerse competitivas. Entre ellas, destacan la rentabilidad, la flexibilidad de diseño y la capacidad de cumplir con los requisitos regulatorios. Al invertir en plásticos personalizados, las empresas pueden optimizar los procesos de producción, reducir el desperdicio de material y crear productos que se ajusten a las tendencias del mercado y las preferencias de los consumidores.
Rentabilidad y escalabilidad
Los plásticos personalizados permiten a los fabricantes optimizar el uso de materiales, reduciendo los costos de producción sin comprometer la calidad. Al adaptar la composición del material y el proceso de fabricación, las empresas pueden lograr economías de escala, lo que convierte al plástico personalizado en una solución rentable tanto para producciones pequeñas como grandes. Esta escalabilidad es especialmente valiosa para las empresas que buscan ampliar sus líneas de productos.
Flexibilidad de diseño para productos únicos
La posibilidad de personalizar cada aspecto de un producto de plástico, desde la forma y el color hasta la textura y el rendimiento, ofrece a las empresas una libertad de diseño inigualable. El plástico personalizado permite crear productos únicos que destacan en el mercado, ya sea un elegante dispositivo de consumo o un componente industrial especializado. Esta flexibilidad fomenta la creatividad y la innovación, permitiendo a las empresas diferenciarse de la competencia.
Cómo se fabrican los plásticos personalizados
El proceso de fabricación de plásticos personalizados implica diversas técnicas avanzadas, como el moldeo por inyección, el moldeo por soplado y la extrusión. Cada método se selecciona en función de las especificaciones y la aplicación del producto deseado. Por ejemplo, el moldeo por inyección es ideal para crear componentes precisos de gran volumen, mientras que el moldeo por soplado se utiliza comúnmente para productos huecos como botellas. Estos procesos se basan en tecnologías de vanguardia que garantizan la consistencia, la calidad y la eficiencia en la producción de plásticos personalizados.
Moldeo por inyección para precisión
El moldeo por inyección es uno de los métodos más utilizados para producir plástico a medida. Este proceso consiste en inyectar plástico fundido en un molde, lo que permite crear componentes con un alto nivel de detalle y precisión. Es ideal para aplicaciones que requieren tolerancias estrictas, como dispositivos médicos o carcasas electrónicas, y permite la producción a gran escala con un mínimo desperdicio.
Moldeo por soplado para productos huecos
El moldeo por soplado se utiliza comúnmente para crear productos huecos de plástico personalizados, como botellas y contenedores. Este proceso consiste en inflar un tubo de plástico calentado dentro de un molde para darle la forma deseada. El moldeo por soplado es altamente eficiente para producir soluciones de envasado ligeras y duraderas que satisfacen las necesidades de industrias como la alimentaria, la cosmética y la farmacéutica.
Comparación de Plásticos personalizados Técnicas de fabricación
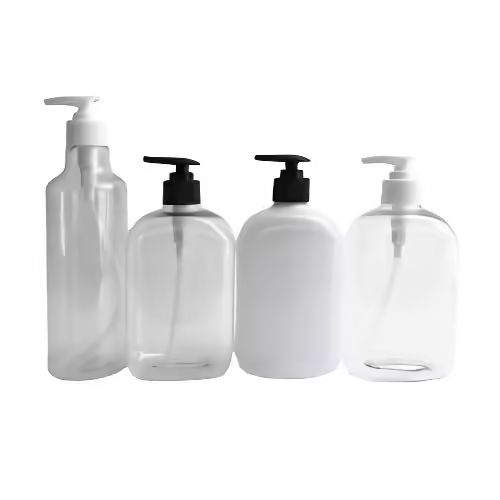
Para proporcionar una comprensión más clara de las opciones de fabricación disponibles, la siguiente tabla describe las características clave de los métodos comunes de producción de plástico personalizado:
Técnica de fabricación | Descripción | Aplicaciones | Ventajas |
---|---|---|---|
Moldeo por inyección | Implica inyectar plástico fundido en un molde para crear componentes precisos. | Dispositivos médicos, piezas de automóviles, electrónica de consumo. | Alta precisión, adecuado para producción de gran volumen, mínimo desperdicio. |
Moldeo por soplado | Forma productos huecos inflando un tubo de plástico calentado dentro de un molde. | Botellas, contenedores, soluciones de embalaje. | Rentable para productos huecos, diseños livianos. |
Extrusión | Empuja plástico fundido a través de una matriz para crear formas continuas. | Tubos, películas, láminas. | Versátil para perfiles continuos, escalable para grandes tiradas. |
Esta tabla resalta la versatilidad de la fabricación de plástico personalizado, permitiendo a las empresas elegir el método que mejor se adapte a las necesidades de sus productos.
El papel del plástico personalizado en el cumplimiento de las normas regulatorias
El cumplimiento de las normativas del sector es fundamental para las empresas, y los plásticos personalizados están diseñados para cumplir con los más estrictos estándares de todos los sectores. Por ejemplo, en la industria médica, el plástico personalizado debe ser biocompatible y esterilizable para garantizar la seguridad del paciente. En el sector de alimentos y bebidas, deben cumplir con las normativas de la FDA para el contacto con alimentos. Al trabajar con fabricantes experimentados, las empresas pueden garantizar que sus plásticos personalizados cumplan con todas las certificaciones necesarias, lo que reduce los riesgos y garantiza su aceptación en el mercado.
Garantizar la seguridad alimentaria con plástico personalizado
Los plásticos personalizados utilizados en envases de alimentos están diseñados para ser seguros en contacto directo con consumibles. Estos materiales se someten a rigurosas pruebas para cumplir con normativas como las de la FDA y las normas de seguridad alimentaria de la UE. Al utilizar plástico personalizado, los fabricantes pueden crear envases que preservan la frescura del producto y garantizan la seguridad del consumidor.
Plásticos personalizados de grado médico para el sector sanitario
En la industria sanitaria, los plásticos personalizados son fundamentales para la producción de dispositivos como jeringas, implantes y equipos de diagnóstico. Estos materiales están diseñados para ser biocompatibles, resistentes a productos químicos y capaces de soportar procesos de esterilización. La precisión que ofrecen los plásticos personalizados garantiza que los dispositivos médicos cumplan con los más altos estándares de seguridad y rendimiento.
Desafíos y soluciones en Plásticos personalizados Producción
Si bien el plástico personalizado ofrece numerosas ventajas, su producción puede presentar desafíos, como la selección de materiales y la gestión de costos. Sin embargo, estos desafíos pueden abordarse mediante la colaboración con fabricantes experimentados. Al aprovechar tecnologías y experiencia avanzadas, las empresas pueden superar obstáculos como la compatibilidad de materiales o la escalabilidad de la producción, garantizando un proceso de desarrollo fluido para productos plásticos personalizados.
Superar los desafíos de selección de materiales
Elegir el material adecuado para plásticos personalizados puede ser complejo debido a la amplia gama de polímeros disponibles. Es fundamental considerar factores como la durabilidad, la flexibilidad y el impacto ambiental. Trabajar con un fabricante experto ayuda a las empresas a seleccionar el material óptimo para su aplicación específica, garantizando así rendimiento y rentabilidad.
Gestión de los costes de producción
Si bien el plástico personalizado ofrece potencial de ahorro, los costos iniciales de configuración de moldes y herramientas pueden ser significativos. Para abordar esto, los fabricantes pueden optimizar los diseños para reducir el uso de material o explorar métodos de producción alternativos, como la impresión 3D para la creación de prototipos. Estas estrategias ayudan a equilibrar la calidad y la asequibilidad en la producción de plástico personalizado.
Tendencias futuras en Plásticos personalizados Innovación
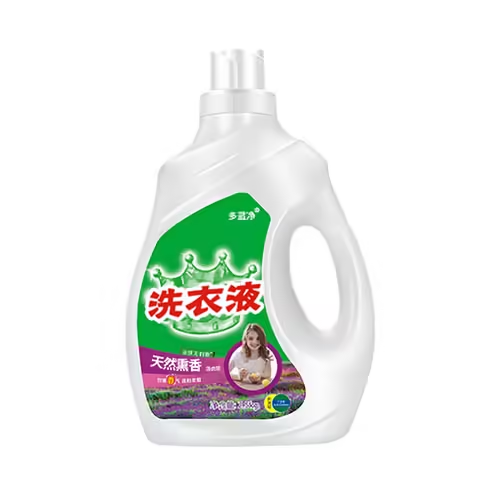
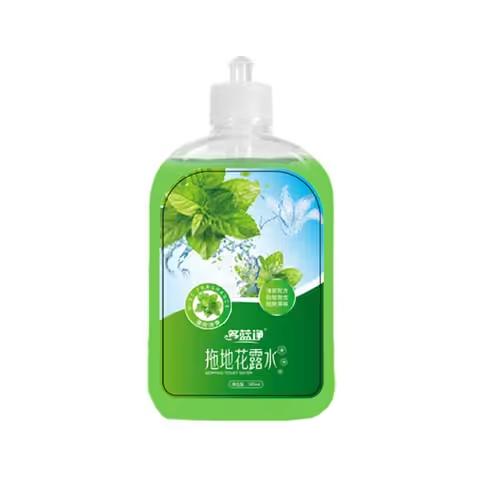
El futuro de los plásticos personalizados es prometedor, con tendencias emergentes como los plásticos de origen biológico, la impresión 3D y los materiales inteligentes que están moldeando la industria. Los plásticos personalizados de origen biológico ofrecen alternativas sostenibles a los polímeros tradicionales, mientras que la impresión 3D permite la creación rápida de prototipos y la producción en lotes pequeños. Los plásticos inteligentes, con sensores integrados o propiedades reactivas, están abriendo nuevas posibilidades en sectores como el sanitario y el automotriz, desplegando aún más el potencial de los plásticos personalizados.
El auge de los plásticos personalizados de origen biológico
Los plásticos personalizados de origen biológico, derivados de fuentes renovables como el maíz o la caña de azúcar, están ganando terreno como alternativas sostenibles. Estos materiales mantienen el rendimiento de los plásticos tradicionales a la vez que reducen el impacto ambiental, lo que los hace ideales para empresas con conciencia ecológica que buscan innovar con plásticos personalizados.
Impresión 3D y plástico personalizado
La impresión 3D está transformando la industria del plástico personalizado al permitir la creación rápida de prototipos y la producción a pequeña escala. Esta tecnología permite a las empresas probar diseños de forma rápida y rentable, reduciendo el tiempo de comercialización de productos de plástico personalizados. A medida que la tecnología de impresión 3D avanza, sus aplicaciones en plásticos personalizados seguirán expandiéndose.
Conclusión
Plásticos personalizados Son un punto de inflexión para las empresas que buscan innovar, reducir costos y satisfacer las demandas de los consumidores. Desde envases sostenibles hasta componentes automotrices de alto rendimiento, los plásticos personalizados ofrecen la flexibilidad y precisión necesarias para mantenerse competitivos en el mercado actual. Con más de 20 años de experiencia en soluciones de envasado y productos químicos de uso diario, Shenlong Packaging se especializa en ofrecer soluciones de plásticos personalizados a medida, desde envases impresos a color hasta moldeo por soplado, moldeo por inyección y fabricación OEM. Tanto si está lanzando su propia marca como si busca productos personalizados, podemos ofrecerle soluciones a medida para satisfacer sus necesidades. ¿Listo para impulsar la innovación con plásticos personalizados? Contáctanos hoy para explorar cómo podemos darle vida a tu visión.
Preguntas frecuentes
Cuáles son plásticos personalizados?
Los plásticos personalizados son materiales diseñados y fabricados para cumplir con requisitos específicos para una aplicación particular, ofreciendo propiedades personalizadas como resistencia, flexibilidad o biocompatibilidad.
¿Cómo se utilizan los plásticos personalizados en los envases?
Los plásticos personalizados se utilizan para crear botellas, contenedores y películas que son livianos, duraderos y diseñados para proteger los productos y al mismo tiempo mejorar el atractivo visual.
¿Son los plásticos personalizados respetuosos con el medio ambiente?
Sí, se pueden diseñar plásticos personalizados con materiales reciclables o de origen biológico para reducir el impacto ambiental y apoyar los objetivos de sostenibilidad.
¿Cómo puedo empezar a utilizar plásticos personalizados para mi negocio?
Colabore con un fabricante experimentado como Shenlong Packaging para analizar sus necesidades y desarrollar soluciones de plástico personalizadas. Contáctenos para comenzar su proyecto.